When Things Go Wrong?
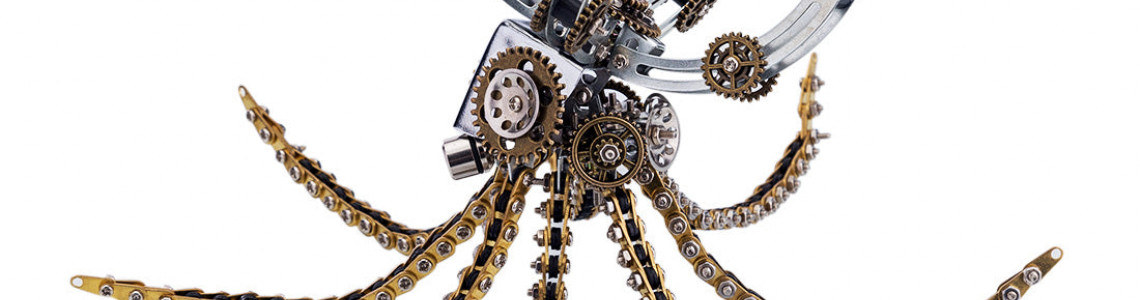
When Things Go Wrong?
Never do I make the same error twice. I typically do it a dozen times or more. And that's the truth of creating Metal Earth models: errors do occur. Only a tiny percentage of my builds were flawless. Given that I've built over 250, I'm willing to wager that I could count them on two hands. I make at least one or two blunders on practically every build, though they aren't all significant, game-changing errors. Even the ones that should be pretty simple.
I usually do this because I was in a hurry and didn't take the time to read the directions. Sometimes, it's because I was having problems fitting two parts together, and a component got flipped entirely. Sometimes, the instructions were written in a location where the laws of physics are different. And occasionally, it was because I'm unfortunate or clumsy—gravity despises Metal Earth models.
But whatever leads to the error, the slip-up, the mishap—it happens. And everyone experiences it. I may have too many of them, in part because a shelf full of models keeps falling on top of another shelf full of models, but I've gained a lot of expertise with errors and breaks as a result.
I'll divide this up into several Things Gone WrongTM categories (I'm not really the owner of a trademark on it, just kidding). In this manner, you can browse the headers and scroll through them if you require guidance on a specific topic. If you have a lot of free time, you can also read the entire thing. Additionally, I've created some narrated videos because some are more complex than my typical fare. I could return and add videos to the post for subjects that don't currently have any.
Quick Aside…
I want to bring up one choice that you may not be aware of before we get started. Metal Earth model manufacturer Fascinations provides free replacement components! Yes, I am aware that it looks absurd in our avaricious society, but they are remarkable in that way. Naturally, I rarely have the patience to wait for replacements to arrive, so I usually make an obstinate effort to continue with repairs. On one occasion, though, I did call them. It happened when I dropped a small piece, and it vanished into the abyss behind my desk. (Believe me, I looked for a long time!) And they were gracious enough to replace it for me even though I hadn't broken it!
The "G" Word (Rhymes with Blue)
If it isn't already in your toolbox, it will likely be in the near future. And, in contrast to what some people may think, there is nothing to be ashamed of. Having glue on hand is not a terrible thing. Although you don't need it to construct these models, it's helpful to have them on hand if you make mistakes frequently, as I do. When you can't get a connection as tight as you'd like, it can be helpful at times, to be honest.
In any case, there are a few possibilities for glue, the two main ones being 5-Second Fix and Super glue. Technically, you can also use clear or white school glue. Just don't, though. It's not a decent answer. It is possible. But only in dire circumstances.
Of course, superglue is the most widely used glue. I typically use the Gorilla Glue Gel Brush and Nozzle; however, there are other brands and forms available. You can utilize cyanoacrylate in almost any form. Just keep in mind that most forms, even if they appear clear when applied, are dry white. Therefore, if you decide to use super glue, you should limit its application to areas that won't be seen.
The 5-Second Fix is another solution that I frequently see people doing. Although there are numerous brands, that is the name I am familiar with. Although it is a UV-cured resin or plastic, it functions similarly to glue. This stuff's best feature is that it dries clear. Its second best feature is that it usually cures in about 5 seconds (like most glues, a complete cure takes longer). However, as it only starts to cure (quickly) when exposed to UV light, you get to choose when those five seconds are. Regretfully, the cost is slightly more.
There are two "tools" that I prefer to use while applying glue and any adhesive. I usually use an essential toothpick. They are inexpensive, disposable, and include an excellent tip that you can precisely apply with a tiny bit of glue. Sometimes, though, even it isn't accurate or small enough. In that scenario, I use the metal wire from the interior of a sandwich baggie or other similar object to make a twisty tie. Naturally, you need to have a very steady hand in certain situations, which is complicated for me, but it's preferable to attempting with a toothpick.
I Broke a Piece Along a Fold
I apologize for the inconvenience. This was the first repair topic for which I attempted to create a video. Since I was assisting in the maintenance of my daughter's model, it would be entertaining to have her watch me work. The theory was that it would make the film more organic as I described what I was doing. How ironic. My darling little Princess Porgie is quite the character and offers plenty of distractions (Squirrel!) along the road. She insisted on having a unique nickname because other builders on Instagram had given my son the nickname Little Code Wookiee. As a result, the video is longer than I had anticipated. Apologies.
Now, I'm not going to forego writing up the process just because I recorded a video. Since I'm much better at explaining things when I have time to think things through and make changes as I go along—for example, I revised that line halfway through and then updated it again later—I decided to establish this blog instead of a vlog. To paraphrase my friend @AnimateOrange, some individuals learn best by reading, others by hearing, and some by seeing. If it's not clear, this blog is most likely more appealing to those who learn best by reading. Although I make an effort to incorporate images wherever possible, I feel more at ease speaking in writing than in person.
How may a broken fold or seam be fixed? Over the past few years, I've tried a few different strategies, but my favourite is the one I picked up from Instagram user @iwallod. These days, I use it virtually exclusively. This approach involves bracing the two sections together with a spare metal piece from a part sheet.
I begin by determining how many braces I will need and where to brace the fractured seam. Since the broken section is usually minor, I need one brace most of the time (longer seams seem to be more durable). In order to achieve the strongest possible bond, I also make an effort to choose a suitable spot for the glue. For obvious reasons, I also make careful not to cover any slots. Asking how I know that is not appropriate. Oh, and I also make an effort to ensure that the surface to which I'm applying the brace won't be seen.
After deciding where I want my bracing, I calculate how long a strip of scrap metal should be to cross the gap without going past the nearby surfaces. From the parts sheet, I cut out a strip of roughly rectangular scrap metal with some flush cutters (or generic wire cutters). Next, I use the cutters to make a "crease" in the centre of the strip or where it will fold. This aids in creating a more acute angle for the fold. Speaking of angles, I strive to fold it to the final angle that the surfaces next to it will have. I don't want to change the angle after glueing because the joint I'm constructing will be somewhat brittle.
The brace or braces must then be adhered to only one side of the seam using glue. You can use anything you like, but I usually use super glue. I make an effort to position the component so that the brace will be glued to a flat surface. For this phase, a used tool can be helpful. I put the bracing strip on the initial surface of the fractured section after applying glue to it. After that, I pause to make sure the second brace half is positioned at the proper angle for the other half of the part. I give it at least an hour or two to dry or cure after I'm confident it will remain that way.
Returning to the procedure, I then glue the brace to the other half of the damaged portion. Since the halves hardly ever cooperate in precisely aligning and remaining that way on their own, it usually tough at this point. In that instance, I genuinely value the used tool since, if the part is large enough, I can utilize the alligator clips to maintain alignment. If not, I hold the parts in place while I sit down and watch a little TV. Or figure up another technique to maintain their alignment. I let the adhesive set or dry overnight once I'm satisfied that it will remain aligned. Most glues, including super glue, take longer than you might imagine to dry completely.
I've now put the pieces back together. It might not be as attractive as it would be if I hadn't broken the seam, and it might not be fully closed. However, it's preferable to simply owning a defective model. However, because the joints are brittle, I take extra care with that section moving forward. In order to avoid putting undue strain on the connection, I keep a tool holding over the component/brace surface if I need to shape the remainder of the part at all.
Also, if I had been thinking, I would have taken pictures while documenting this procedure. Video screenshots wouldn't work well as graphics for this section. The next time I have to do this—when not if—I'll try to snap pictures and add them to this area.
I Broke a Tab Off
In my experience, this has happened to me 90% of the time because I twisted the same tab, untwisted it, and then twisted it again. Most likely as a result of my incorrect advice. More specifically, because I didn't pay close attention to the directions, the outcome is the same. Well, it can be frustrating no matter how you break a tab off.
Depending on where and how the tab is utilized, you have several choices for clearing this up when it occurs. My first choice is to merely glue the tab if it's an internal tab, meaning it won't be visible after the model is finished. I glue it as discretely as possible if it's an outside tab. With some restrictions, that's only one choice.
If the glue isn't hidden deep inside the model, it should be easy to apply to the internal damaged tabs. If the item isn't already attached, I start by securing it with any remaining tabs, being careful to line up the tab remnants in the slot. Even if there might not be much left, something is typically there. I then give the back of that slot a tiny bit of adhesive. It may get stuck in the slot and accumulate on the outside if you use too much of it. In order to force the glue to defy gravity and wick to the outside, I also attempt to rest or hold the assembly. An alternative that is quicker and dries clear (so you don't have to worry about it showing from the outside) is a 5-Second Fix. After the first day dries well, I will apply more glue if the connection needs a little reinforcement.
I use one of two methods for externally damaged tabs: either use some clear glue or secure the sections with a scrap metal brace. I modified the procedure outlined in the previous part; I Broke a Piece Along a Fold for the scrap-metal brace. I only do this, of course, when I can conceal the brace within. Although I'm a little embarrassed to admit it, I've used Elmer's clear school glue in the past, but I like to use 5-Second Fix for clear gluing because it produces the strongest bond. You have to do what you have to do, even though it's not a firm grasp.
Additionally, you can always ask Fascinations for a replacement if neither of those options is feasible or effective. Although it is an option, I avoid doing that as much as possible.
I Forgot to Attach a Piece
I feel like such an idiot when I do this, man. I either didn't notice it, skipped it by accident, or missed it for some other stupid reason. I frequently attempt to dismantle the model as far back as is necessary. However, there are risks involved, particularly if the tabs have been twisted (which is why I recommend folding tabs instead of bending). Unfortunately, twisting is sometimes unavoidable. Sometimes, it was nearly difficult to twist in the first place, so untwisting is not an option. Naturally, untwisting also carries the risk of shattering a tab (see previous section, hehe). For whatever reason, I do the following if I don't want to disassemble:
Yes, another narrated walkthrough video! Additionally, it features Princess Porgie (the same model and taping period as the Broken Folds video). I apologize for her depression; she was energized by her ADHD and thrilled to be a part of this. Don't worry—I'll give you a brief recap in words if you don't want to watch the video!
Here, I choose a straightforward method: I simply apply the tiniest dots of super glue to the slots (in the actual air gap) and then push the tabs through the glue. I've discovered that using a twist-tie's metal core is the most accurate method for applying that tiny bit of adhesive. However, I prepare the components so they are fully ready to join before I use the glue. Additionally, I angle the tabs slightly inward before folding them. While the super glue cures, this offers a straightforward mechanical grip to keep the part firmly in place. I then put glue in the slots and attached the component. Sometimes, you're stuck holding it, but the tab tilting may let you put it away to dry. Of course, you may also use 5-Second Fix with most glue applications. Because it dries transparent in this instance, you can apply a bit more.
I Attached a Piece Backwards
This occurs—a lot. Perhaps I'm the only one. Maybe I become too eager and start moving too quickly. MaybeI may not have followed the directions carefully enough. Or perhaps I'm listening, but in all my tries to get the dreaded parts to fit together, I'm having so much trouble aligning that it ends up being misaligned or turned around! Alright, relax, breathe, everything will be fine. Naturally, it doesn't always end up backwards; it could be sideways, 90 degrees rotated, or anything else. I selected that as the most typical illustration of this issue.
The fact that I do this so frequently reminds me of something I've mentioned multiple times in this post: I fold tabs whenever I can, especially on tabs that are inside. Please be patient with me as I give you some unasked-for advice: fold, fold, fold! Because unfolding is much simpler than twisting when you need to reverse some work to remedy something. But sometimes, the only thing you can do is twist. If that's the case, I suggest that you avoid entirely twisting every tab. It should be simple to determine which way to untwist a tab if you have to do so. I'll now give you some advice on how to remove associated parts carefully.
Let's start by discussing unfolding tabs. As part of my bizarre Instagram post about my fictitious love affair with a hobby knife as a building tool, I shared a video (above) that I produced some time ago. Fortunately, this video is brief, audio-free, and should demonstrate how useful it is as a tool for tab unfolding without causing any harm to the model. I frequently begin the unfolding operation with a hobby knife and complete it with tweezers to prevent scratches. You can separate the components and straighten out the tab with greater leverage when using tweezers.
My two main recommendations for untwisting are to (1) be gentle and (2) make sure you untwist correctly. Twisting causes broken tabs considerably more often than folding and weakens the metal much more (at least for me). Additionally, it will be nearly impossible to separate the parts if you twist the tab incorrectly. Sometimes, it isn't easy to discern which direction you turned a tab, but sometimes, a magnifier (or the camera on your phone) can help. To make the part release as readily as possible, I like to use tweezers or pliers to grasp the tab at its full height and squish it as flat as I can after untwisting. But occasionally, the little twist is all that keeps the pieces together. In order to work the component free, you can begin at one end of the edge where the two sections mean and attempt to slowly and gently insert a [dull] hobby knife into the space.
I advise you to flatten the tabs out after separating the sections, regardless of how you do it—all the way to the tab's bottom. Even with your best efforts, some deformation may still occur after the separation. Therefore, it will be easier to reattach the parts if you flatten them as much as you can. Additionally, be careful not to reattach it in the exact wrong orientation. Avoid being like me! You'll feel so stupid. It will likely take a bit more effort to seat a twisted tab completely when you re-insert it.
I Scratched the Paint
That sensation when your hold falters and... Scratches has an unpleasant odour. And everyone experiences them at some point. Additionally, scratches on multicoloured models are more noticeable. But don't worry! Actually, there is a relatively simple method to hide your transgressions, and I discovered it from a number of sources on Reddit and Instagram. I want to give them all credit if I could recall who it was. In any case, Sharpies (or other permanent markers) are the easy fix. The majority of Metal Earth's colours are surprisingly near to sharpie hues or close enough that they are less noticeable than the underlying metal colouring.
In terms of methodology, I perform a few things to minimize the visibility of the repair. I start by keeping my own set of coloured Sharpies out of the reach of kids. Kids often mash the Sharpie tip into a more rounded shape, so I want to keep it nice and pointy. Second, instead of stroking, I tap or dab the ink on. Because of the metal's smoothness, the sharpie may streak when drawn across the surface, leaving some areas with more ink than others. Additionally, tapping (lightly) enables me to apply the ink more carefully and precisely.
As an aside, some of the ugly folded tabs on the surface of coloured models can also be "hidden" using this technique. I'm referring to the situation where you have to fold a tab silver-side out, and it protrudes sharply against the coloured surface you folded it against. It can be nearly erased with a few Sharpie dabs. It has an unexpected impact. A set of metallic Sharpies (silver, gold, and bronze) was also purchased by me in case a coloured tab gets folded up into a silver or gold surface. I rarely use bronze.
I don't have a magic fix for scratches on models that aren't multicoloured or printed in colour. The best course of action is to spin the model if the scratch is in the metal rather than the paint. Call it weathering, war damage, or anything like that. However, be aware that you are not alone in doing so—greetings from the family.
Bent Up in Package
One unfortunate aspect of these models is that they can occasionally arrive already damaged. Sometimes you have to start from a sheet of pieces that have been well and battered up, regardless of whether it was anything that happened during shipping, the mail, or another circumstance. Only a tiny portion of the sheet has been slightly creased forward. Or possibly there are multiple bendings and back and forth, giving the impression that the model has been partially crushed. It occasionally occurs, mainly if you buy it online. However, there is still hope!
A C-size battery is my first choice when I run into this issue at the start of construction. Using my hands, I attempt to flatten the parts sheet into a loose shape. I then placed it on a smooth, level, and hard surface, engraved side down. I then repeatedly roll the battery across the top of it. I turn the sheet over and roll again, applying a reasonably firm press each time. I occasionally leave the sheet slightly bent, so I turn it over and gently roll it over a couple of times.
Unless the fold was extremely sharp or anything was scraped, this usually fixes all the damage and restores it to a usable condition. Although it won't be flawless, you'll probably be the only one who notices it because you're aware of its existence. On a few occasions, I had to move on from this and smooth out some thinner sections with a hobby knife. One of these involved the London Eye model's "wheel spokes." I eventually got it to a respectable level, but it required a lot of patience and a few curse words.
I Lost a Piece!
First things first, see if the sheet has an extra piece. This advice ought to come before a few of these parts, but I'm including it here, so here it is. My additional tip might be too late if there isn't an extra piece.
Because that piece of advise is to keep all of your spare components in storage. There will frequently be some parts left over after completing a project. And I threw those and the scrap metal frame away when I first started. However, I now save the scrap metal frame and spare parts. I maintain the extra parts for this purpose (and for other, more creative activities, as well), but I keep the frame for when I might need to create a brace (or for other, more... creative endeavours).
In fact, we discovered that Princess Porgie had unintentionally misplaced one of the pieces of her Minnie Mouse model after we had finished filming the two movies with her. She was devastated. But I found a part that matched closely enough (surprisingly, it was simply an extra tab slot!) that we could use after taking it out of my spare parts bag. Naturally, I have a lot of parts in that bag that don't seem to be useful, but you never know when they might be needed, mainly if you fall victim to the "mod" craze and begin making your own personalized Metal Earth models (creative undertakings, indeed!).
It's Beyond Recovery
Alright, so occasionally, an error or mishap can render a model irreparable. And believe me, I've experienced this myself. And it's awful. If you'll stay with me, though, it might not be a complete loss. It could simply be a chance to exercise your creative side.
The first model that indeed went wrong for me was one that I finished. However, I didn't finish it well. The "wings" on that model, which was the original TIE Fighter model, were just poorly attached. It was discovered that it was partially because it was a copycat model and that the quality was subpar (I didn't plan on purchasing a knockoff, but I hadn't learned to exercise caution when buying models on eBay—avoid Chinese goods!). In any case, the final product was incredibly janky and shaky. It simply looked terrible. It wasn't very comfortable until I discovered a method to reverse it.
In my yard, I put it out. And I used a BB gun to shoot it. I then attempted to use a lighter to burn it. That didn't work out so well, so I set it all on fire and buried it in a heap of leaves. Did you know that when superglue burns, it loses its ability to stick? Yes, exactly. It remained unsteady despite being superglued. Well, it came apart when I burnt it. I, therefore, put it back together and reglued it. Which indicates that I wasn't merely venting my rage.
Then, I grabbed a small puck of floral foam. I carved some slots into the top and gently curved the top to resemble the TIE fighter's wing span. I then painted the top tan and the bottom black. After that, I "dusted" the top with sand and applied some spray glue. After doing this several times to achieve a thick layer of sand, I positioned the wing panels into the slots, keeping everything at an angle. Then, where the wing panels and foam met, I ran a thin line of clear school glue around the edges—another sand-dusting. Scatter the entire surface with sand, then see where the sand gathers on the model. Sand should be brushed off; then thin adhesive should be applied where necessary. Fill the cockpit with sand. Additionally, one of your TIE fighters crashed in the desert! Redeemed failure!
And I didn't take that path just once. I recreated the crash sequence from Star Trek: Generations and removed the Saucer Section to salvage my first version of the TNG Enterprise, which balanced horribly. Additionally, I have another project, the Sydney Opera House, where a number of crucial components broke in two, and no adhesive strip could withstand the strain where they broke. When I get the urge to do it, I'll put that aside and turn it into a set piece for a catastrophe movie. The only model I haven't wholly redesigned is a BB-8 model that was trampled underfoot. I was unable to think of anything original to do with it.
Therefore, you can use that unavoidable accident as inspiration to develop a distinctive modified version of the model. Or ask for some replacement components. Or, if you'd like, throw it away. However, have an open mind! You may have a diamond in the rough.
Interaction!
I've started adding an interactive element at the end of my postings—some inquiry or invitation to participate. Although I suppose that's not a bad thing, this isn't some plan to increase blog activity. No, it's because I'm aware that I'm not an expert. I'm always picking up tips from other builders on Reddit, Instagram, and other sites. Why not here, then? And it's already shared with others since it's here, right?
In any case! These are simply the mending techniques I've discovered. I'm aware that every builder has created their methods and approaches, and I'd be interested in learning them. Please leave a comment below if you have a different solution for any of the situations above. Please let us know if you have come across a problem that doesn't fall under one of the categories above, regardless of whether you have a solution for it.